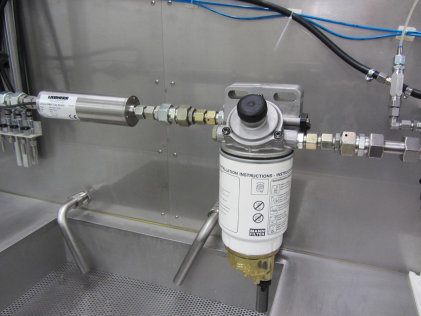
Litronic FMS RMH12 pipe sensor
The Liebherr in situ water content determination Litronic-FMS III-RMH12 is used to detect the water content (concentration determination) even in very low ppm ranges in emulsions such as diesel fuel, transmission, hydraulic, engine, roller bearing, transformer and turbine oil as well as in battery systems.
The sensors were developed in cooperation with the ISO/TS 16332 standardisation committee for the water separation ability of diesel fuel filters.
The installation takes place on test and inspection stands and replaces the previous manual sampling as well as other offline measuring systems.
Measurement by the Liebherr sensor system is based on the physical principle of capacitance determination in the high-frequency stray field.
In addition to their high precision and robustness, the measuring devices from Bad Schussenried are characterised by their reproducibility.
Once the system has been calibrated, further measuring points can be set up or devices renewed on this basis at any time without great effort. The plant thus always remains reliable, regardless of its previous term and age.
Benefits
- Indirect measuring method: Capacity determination in the high frequency stray field. This method uses the different dielectric constant (permittivity) of water and liquids.
- Fully reproducible sensors: If the plant is subsequently extended with sensors or if sensors are replaced, no recalibration is necessary thanks to the built-in microprocessor.
- Process control and regulation: Thanks to extensive interfaces, the moisture measurement can be integrated into process control systems and controls.
- Cost saving: Time-consuming and costly laboratory analyses are no longer necessary or can be reduced.
- Temperature measurement/temperature compensation: The sensor can also be used to determine the temperature of the medium.
- Limit values: Maximum or minimum limits can be set using the software. Light or sound signals can be triggered if required.
- Mean value calculator: The sensor passes on already averaged values to the FMS evaluation and transfer module.
- Material flow: The entire liquid is measured (coaxial capacitor).
- Rapid reaction time: The sensor measures 30 times a second and passes on already averaged values to the evaluation unit.
- Measurement accuracy: Stable, extremely high measurement resolutions of up to 3 ppm are possible.
- High-quality materials: The use of high-quality materials is also reflected in the resistance to a wide range of oils.
- Software and evaluation and transfer module: The mandatory software integrated in the Litronic-FMS evaluation and transfer unit is used for recording, processing and preparing the values measured by the sensors, parametrisation and calibration. In addition, the unit offers graphic visualisation and further signal transfer to higher-level controls.
Physical principle |
Coaxial field in a cylinder condenser |
Frequency |
20 MHz |
Measurement location |
Pipe diameter 12 mm |
Process connection |
Ermeto cutting ring screw connection 12 mm, M18x1.5 |
Measuring range |
0 – 100 % water content, measuring window adjustable |
Capacity resolution |
250 aF |
Update cycle |
33.33 ms |
Maximum attainable measuring accuracy |
+/- 10 ppm water content 1.) |
Measurement value transfer |
digital: RS-485, streaming |
Max. number of sensors on the bus |
4 |
Maximum bus length |
1200 m |
Power supply |
12-24 V, 0.5 VA |
Temperature measurement measuring range |
5 – 90 °C |
Operating ambient temperature |
5 – 60 °C |
Storage temperature |
-40 – 60 °C 2.) |
Protection class |
IP65 |
Max. pressure |
6 bar |
Volume flow |
5 - 1200 l/h |
Connection line length/type |
UNITRONIC® ROBUST C 7x0.14 shielded/6 m |
Housing material |
V4A (1.4305) |
Dimensions: Ø/Length |
54/219 (230) mm |
Weight without cable |
approx. 2.1 kg |
1.) with ideal flow behaviour and proper calibration
2.) free of liquid
Characteristics
- Direct digital measuring process.
- Extremely high capacity resolution due to patented measuring circuit
- 30 measurements per second enable assessment of the dynamic behaviour
- Automatic reference equalisation every second
- Temperature-stabilised, regulated quartz time base (TCXO)
- High-resolution temperature measurement/compensation of the liquid.
- High-resolution temperature measurement/compensation of the measuring circuit.
- Extremely high water resolution due to optimum geometry of the coaxial condenser.
- Ceramic coaxial condenser.
- High quality stainless steel housing.
- Resistant against aggressive liquids/oils.
- Flow-optimised throughput with even cross-section.
- Simple process connection.
- Digital interface/networking.
- Data-streaming technology with automatic bus arbitration.
Documentation
flyer-litronic-fms-rmh-en
data-sheet-litronic-fms-rmh-12
rmh-animation-d-e