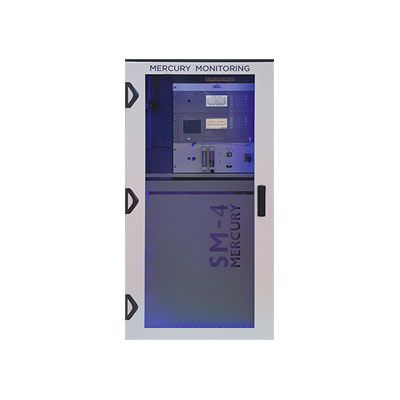
Total mercury emissions monitor in stack flue gases, qal 1 certified SM-4
QAL 1 certified for continuous, accurate and reliable measurement of total mercury emissions, even in very low concentrations and within complex matrices (SO2, NOx, HCl, etc.)
With over 20 years experience, Mercury Instruments (part of ENVEA Group) were the first to develop mercury monitors and mercury analyzers using a dry thermocatalytic method instead of wet chemistry.
The SM-4 Mercury Monitor is QAL1 certified and is ready to meet future regulatory requirements (Minamata convention & European directives for thermal power plants and incinerators).
FEATURES & BENEFITS
- Automatic and continuous monitoring of total mercury emissions in stack flue gases. QAL 1 certified
- Extremely high precision and reliable measurement
- Automatic back-flush function
- Continuous measurement of total Hg (elementary, ionic & organic)
- No liquid waste or condensate generated
- Sample dilution directly at sampling point, allowing for large measuring range & elimination of interferences from matrix gases, no transport of ionic Hg
- Sampling system – composed of the probe, the dilution unit and the low temperature catalytic converter – is entirely heated to avoid mercury adsorption
- Very low maintenance (service interval: ≥ 3 months) – can be automated
- Ultra high sensitivity: low measuring range is 0.05 µg/m³
- Approved and certified by TÜV Rheinland (QAL1)
- Main options:
- Mercury speciation
- Elemental Hg calibration gas generator NIST traceable, installed inside the analyzer cabinet
- Automatic calibration systems (oxidized and elemental)
- Automatic QAL3
- Sampling line length up to 100 m (300 ft)
MAIN APPLICATIONS
Mercury monitor perfectly adapted for continuous mercury analysis in:
- Coal fired power plants (before & after mercury absorbers)
- Emissions monitoring for facilities under 13. and 17. BImSchV
- Cement kilns
- Sulfuric acid producing foundries
- Waste Incineration plants (industrial, medical waste, sewage sludge…)
- Thermal treatment of contaminated soils, hazardous waste
- Metallurgical facilities with potential Hg emissions…
TECHNICAL SPECIFICATIONS |
Measuring principle |
thermocatalytic reduction at stack, Amalgamation (MI GoldTrap), cold vapor atomic absorption (CVAAS) at 253.7 nm |
Measured component |
Total mercury (ionic and elemental speciation as option) |
UV-Source |
Electrodeless low pressure mercury lamp (EDL) |
Stabilization method |
Reference beam method |
Optical cell |
Fused silica (Suprasil), l: approx. 230mm, heated approx. 45° |
Measuring ranges |
0.05 μg/m³ – 500 μg/m³ Hg (up to 1000 µg/m³ as an option) |
Detection limit |
0.0001 μg/m³ (Detector); < 0.01 μg/m³ (System) |
Response time T90 |
180 – 360 sec |
Calibration |
– automatic, with built-in calibration gas generator for elementary Hg (option); – automatic, with built-in calibration gas generator for ionic Hg (option); – manual, with built-in heated fitting to connect externally provided calibration gas (e.g. HOVACAL®) |
TECHNICAL DATA |
Signal outputs |
analogue: 4-20 mA (500 Ω max.); serial: RS232; Modbus RTU/RS485 (option); Ethernet (option) |
Status output |
3 x pairs of relay contacts (dry contacts) |
Remote access |
Modem and SM-4 software (option) |
Max. sample temperature |
250 °C (others upon request) |
Ambient temperature range allowed |
-5 to 40 °C |
Sample line length |
up to 30 m (up to 100 m option) |
Power supply |
230 VAC / 50 Hz (110 VAC / 60 Hz option) |
Electrical Power consumption |
Analyzer cabinet: 450 VA; Probe-converter unit: 1000 VA; heated sample line: 30 VA / meter |
Dimensions (H x W x D) |
Analyzer cabinet: 161 x 80 x 60 cm; Probe converter unit: 36 x 36 x 66 cm; Probe controller: 48 x 44 x 27 cm |
Weight |
Analyzer cabinet (including automatic calibrator): 130 kg; Probe converter unit: 28 kg; Probe controller: 14 kg |
APPROVALS & CERTIFICATIONS
Compliance with:
- US EPA 40CFR60 PS-12A Mercury CEMS;
- Minamata convention & European directives for thermal power plants and incinerators
- EN 15267 (European regulation);
- Industrial Emissions Directive (IED)
- Integrated Pollution Prevention Control (IPPC) Directive,
- Large Combustion Plant Directive (LCPD)
- Medium Combustion Plant – MCP Directive (EU) 2015/2193
- Waste Incineration Directive (WID)
- Approved and QAL 1 certified by TÜV Rheinland Energie und Umwelt GmbH, Köln, (QAL1)
Our mercury analyzers are manufactured according to the ISO 9001 quality regulations.
CE approved
Documentation
envea_catalogue_cems_emission-monitoring_en
SM-4_Mercury_Stack_Gas_Monitor_EN_1019
ENVEA_Process_Catalogue_EN