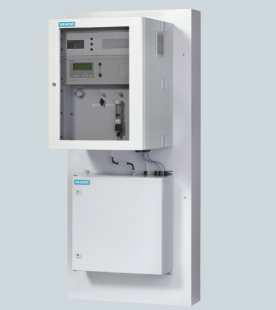
Set BGA (Bio Gas Analyzer) is a fully configured and ready-to-run gas analysissystem for use in biogas plants. The integrated ULTRAMAT 23 industrial gasanalyzer has four measuring channels for simultaneous determination ofthe relevant gas components methane, carbon dioxide, hydrogen sulfide,and oxygen. The Set BGA is especially economical for the operator thanks tostandardization. The ULTRAMAT 23, proven in decades of harsh industrial use,features maximum performance and operational reliability.
Biogas - production and use Biogas is a flammable gas used for generating energy; it is produced by fermentation of biomass under exclusion of oxygen. Such plants can be found in agricultural companies and also in municipal or industrial sewage treatmentplants. The materials used include organic municipal waste,renewable raw materials, liquid manure. The crude biogas produced ina first reactor (fermenter) consists of methane and carbon dioxide as the main components as well as hydrogen sulfide, ammonia and water vapor (see table "Biogas composition"). The flammable methane is the supplier of energy. Following further treatment, the biogas is used in combined heat and power (CHP) plants with gas engines to generate electricity and heat or is fed into a natural gas network.
Gas analysis in biogas plants A biogas plant must be continuouslymonitored with respect to gas composition, temperature, dwell time in the fermenter and the addition of substrate to ensure optimum operation of the biological process and to achieve as high a methane yield as possible. It is particularly important to check the concentration of hydrogen sulfide as this residual gas is toxic and corrosive and can also disrupt the biological process above a specific concentration level.Plant monitoring is carried out by analyzing the composition of the raw biogas downstream of the fermenter with the following significance for the process:
• The methane concentration is used to control the addition of material.A fluctuating methane content in the fermenter would considerablydisrupt the fermentation process.
• The oxygen concentration is extremely important to ensure anoptimum fermentation process since the formation of explosivegas mixtures can then be detected early and prevented.
• Measuring hydrogen sulfide levels makes it possible to keep theconcentration of this toxic and corrosive gas as low as possible bytaking appropriate action. Besides the risk to people resulting fromits toxicity, this gas can adversely affect both the generation of biogasand downstream processes.
• Under the effects of humidity and warmth, hydrogen sulfide reactswith metal components such as pipelines or connections. Whenhydrogen sulfide is converted to sulfur dioxide in combustionengines, this endangers their operational safety and makesmore frequent oil changes necessary. The metallic heat exchangerinstalled downstream can also be damaged.
Documentation
Gas analysis in biogas plants with
the "Set BGA" complete measuring
system from Siemens